Accurate construction estimating is essential for the success of any building project. Whether you’re a contractor or a project manager, mastering the art of estimating helps you avoid budget overruns, delays, and mismanagement. In this blog, we’ll explore the 5 golden rules of construction estimating that every professional should follow to ensure project success.
1. Thoroughly Understand the Project Scope
The first golden rule of construction estimating is to thoroughly understand the project’s scope. Without a clear understanding of the scope, your estimates could miss critical elements, resulting in inaccurate cost projections and unexpected expenses. A comprehensive scope of work should include every detail about the project, from material specifications to labor requirements and timelines.
Before starting any estimate, it’s important to review all project documents, blueprints, and specifications. Meet with stakeholders such as architects, engineers, and clients to clarify any uncertainties. Misunderstanding the scope of work can lead to underestimating the resources required or overestimating costs, both of which can result in budget problems.
Pro Tip: Create a checklist that covers every aspect of the project, such as site preparation, permits, materials, labor, equipment, and unexpected contingencies.
2. Use Accurate and Up-to-Date Data
Accurate data is at the heart of a good construction estimate. Whether it’s material prices, labor costs, or equipment rental fees, using outdated or incorrect data can severely skew your estimate. Construction costs fluctuate due to market demand, inflation, and supply chain issues, so it’s vital to have access to real-time data when preparing your estimates.
Make sure your cost databases are up-to-date and regularly review vendor pricing for materials and services. For labor, consider local wage rates and availability, as labor costs can vary significantly depending on the region and the time of year.
Pro Tip: Use construction estimating software such as Bluebeam, CostX, or Kubla to access real-time data and automatically calculate accurate estimates. These tools are also useful for adjusting estimates as prices change during the project.
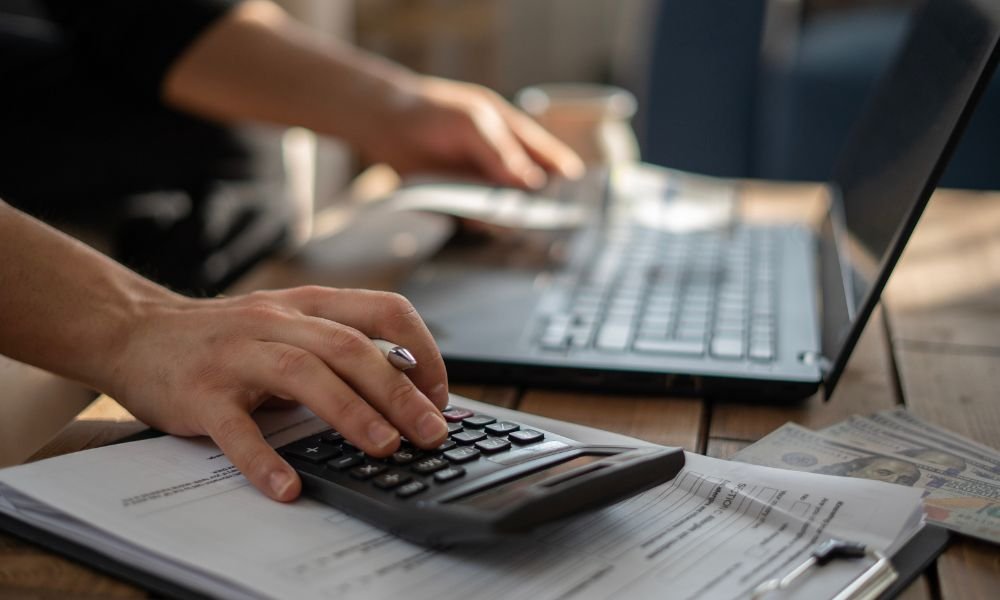
3. Account for All Costs, Including Hidden Ones
One of the most common reasons for construction projects going over budget is the failure to account for hidden costs. These costs often include permits, inspections, site preparation, waste removal, and utility connections. Although they might seem minor compared to major expenses like materials and labor, they can add up quickly.
Hidden costs can also arise during unforeseen circumstances, such as delays due to weather or unexpected changes in design. It’s important to include a contingency allowance in your estimate to cover these potential extra costs. A contingency of 5-10% of the total project cost is recommended for most construction projects.
Pro Tip: Include line items for every possible hidden cost in your estimates and always prepare for worst-case scenarios with a well-thought-out contingency fund.
4. Get Input from Experts and Collaborate with Your Team
Construction estimating is a collaborative process that often requires input from various stakeholders. Estimators should work closely with engineers, architects, contractors, and suppliers to gather accurate data and insights. By involving different experts, you can ensure that every aspect of the project is considered, leading to a more accurate estimate.
Collaboration also helps identify potential problems early in the process. For example, an engineer might notice a structural issue that could increase costs, or a contractor might suggest a more cost-effective way to source materials. Frequent communication with team members ensures that all project needs are addressed and that the estimate reflects real-world conditions.
Pro Tip: Schedule regular meetings with your team and stakeholders to review the estimate and make adjustments based on their input. This can help prevent costly errors or omissions in the final estimate.
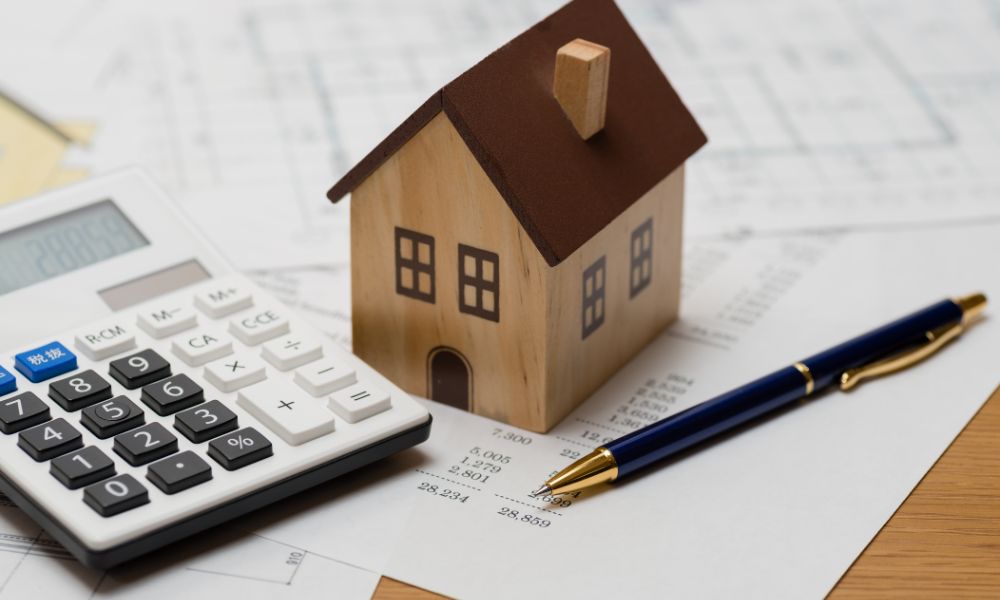
5. Review, Revise, and Update Your Estimate as the Project Evolves
Construction estimates are living documents. As the project progresses, the scope, materials, and labor requirements may change, necessitating revisions to the estimate. A good estimator reviews the budget regularly and updates the estimate to reflect any changes. This could include price fluctuations for materials, labor shortages, or changes in project specifications.
Updating your estimate as the project evolves helps prevent significant budget overruns and ensures that all stakeholders are aware of the project’s financial status. It’s also essential to communicate these updates to the project owner or client to maintain transparency and trust.
Pro Tip: Revisit your estimate at key project milestones and adjust accordingly. By keeping your estimate up-to-date, you can anticipate financial changes and address them proactively.
Mastering the Art of Construction Estimating
The 5 golden rules of construction estimating—understanding the project scope, using accurate data, accounting for hidden costs, collaborating with experts, and regularly revising the estimate—are key to delivering successful projects on time and within budget. By mastering these principles, you can ensure more accurate estimates, reduce financial risk, and increase the likelihood of project success.
At Residential Estimating, we specialize in delivering precise and detailed estimates for residential construction projects in Australia. With our industry expertise and commitment to accuracy, we help contractors and homeowners alike stay on budget and avoid costly surprises. Contact us today to learn more about how we can support your next project with professional estimating services.